Digital technologies are radically changing the ways companies manufacture products, the business models they adopt and how they innovate.
“Digitalisation enhances productivity by automating repetitive tasks and optimising workflows through real-time data analytics,” explains Pat Phibbs, managing director of ALS Identify, a specialist in the design and building of custom labelling and identification systems.
Automated systems can monitor production lines, predict maintenance needs and adjust operations to minimise downtime and maximise output. Quality improves as digital tools such as artificial intelligence ensure consistent standards, detect defects early and reduce waste, he says.
“Errors happen all the time but in food and pharmaceuticals, it is critical that they are caught and caught quickly. Digitalisation facilitates this and saves manufacturers from costly mistakes. On one line, with auto-ID systems, products can be checked at key stages of production to catch mistakes,” he adds.
The key technologies he is seeing among customers are AI and IoT combined. “Internet of things enables real-time monitoring and data collection along the production line. For production managers, rather than working off a plan based on historical data, they can see, in real time, what the production output is on their digitalised production lines,” says Phibbs.

“AI can take that data to detect errors quickly and rectify them to reduce waste and downtime. The additional result of these technologies is that the human workforce now has more time to upskill and can be redeployed into roles that require more human intelligence and intervention.”
To reduce supply chain risk and volatility, it is essential for manufacturers in Ireland and beyond to unlock the power of data analytics, AI and machine learning (ML), says Alan Dickson, partner, supply chain and operations, at accountancy firm EY.
Data analytics and ML provide the heightened level of visibility required to predict and mitigate risks accurately and efficiently, he adds, pointing to the creation of electronic batch records in the life science industry as a case in point.
“Once digitised, this allows for real-time data tracking and analysis. This is crucial for both compliance and quality control, as well as the ability to respond to irregularities in production,” says Dickson.
EY recently worked with a global pharmaceutical firm on such a digital transformation project.
“By integrating cloud technology and IoT solutions, we enabled real-time monitoring of each production batch, significantly reducing batch loss,” Dickson explains. “This provided timely alerts to technicians and operational leads when batches exceeded predetermined time limits, enabling them to proactively spot potential issues.
“Additionally, the transition from paper to digital batch labelling minimised the risk of contamination, further enhancing production integrity and provided a solid foundation for their future new paperless manufacturing plant currently under construction.”
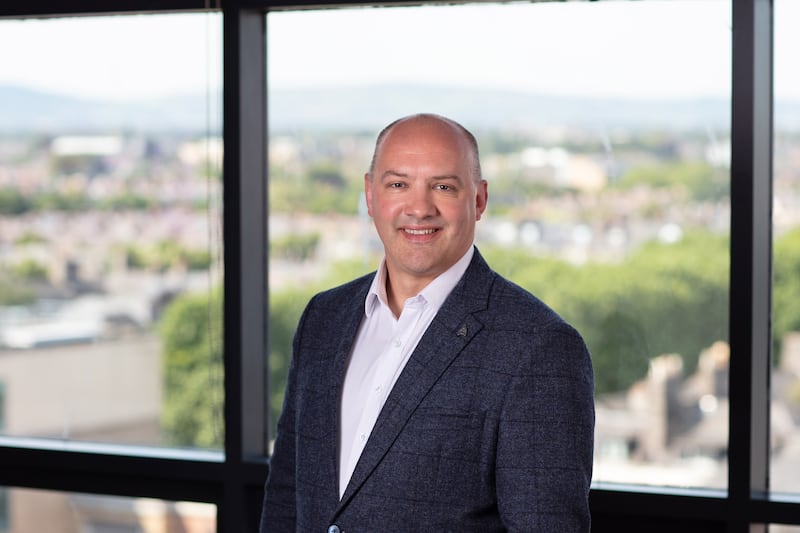
It’s an example of increasing IT-OT convergence. “Traditionally, information technology [IT] and operational technology [OT] operated independently of each other but as the world becomes ever more interconnected this is no longer viable. Manufacturers must leverage the convergence between IT and OT to optimise their manufacturing processes,” says Dickson.
Digitalisation allows manufactures to plug each piece of kit on a production line into software that makes it visible, measurable and manageable.
Before digitalisation, all such data stayed locked in the machine, says David Mulryan, product and marketing director at IFM Electronic. The German headquartered, family-owned business employs 8,000 people and started out providing pressure sensors and flow meters. Today it is helping its manufacturing clients to digitalise their entire manufacturing process.
The insights digitalisation brings are of immense value, says Mulryan, pointing to traditional activities where, for example, someone on a bakery line might have had a chart recorder or data logger beside each machine which, when combined with a quick “squeeze of a muffin”, would allow product to pass quality control, he explains. Now the managing director in the office can see a product’s progress for him or herself, in real time.
IFM‘s new EdgeController product provides flexible digitalisation. As well as facilitating exchange of data between industrial control systems and cloud platforms such as AWS, Azure and AnyViz, it also provides freely programmable control functionality and versatile visualisation options in a single compact unit not much bigger than a mobile phone.
All of this can contribute to a manufacturer’s ESG responsibilities too, by boosting predictive maintenance and helping to eliminate waste and rejects.
Unfortunately what too often holds them back from fully embracing digital transformation is misplaced fear around the costs involved, often allied to a shop floor culture that fears change and prefers to retain the status quo.
In fact, making such changes is easier and more cost effective than people might think. Mulryan points to traditional flow metes as a case in point. These are used to measure the flow rate of a liquid from one machine to another, measured in pulses and analogue signals.
IFM‘s IO-Link protocol products allow for communication between such machines, facilitating bidirectional data exchange between a master device, actuators and sensors.
IO-Link, which is the foundational technology of the industrial internet of things (IIOT), is a digital communication network that provides raw sensor values for more accurate data from machines and eliminates the need to scale analogue signals.
“This protocol can speak to standard input cards of a control system and very simply get a huge amount of data that’s very important to the customer,” says Mulryan. “Now, instead of just seeing on the flow meter how much water has gone into my machine, I can see what temperature it is, how hard it is, and even measure its conductivity.”